A few days ago, Luo Bearing received the largest domestic diameter 13.85 meters, weighing 65 tons of integral three-row cylindrical roller combination bearings successfully off the line, loaded and sent to users.
The product once again set a new record for the largest integral turntable bearing in China!
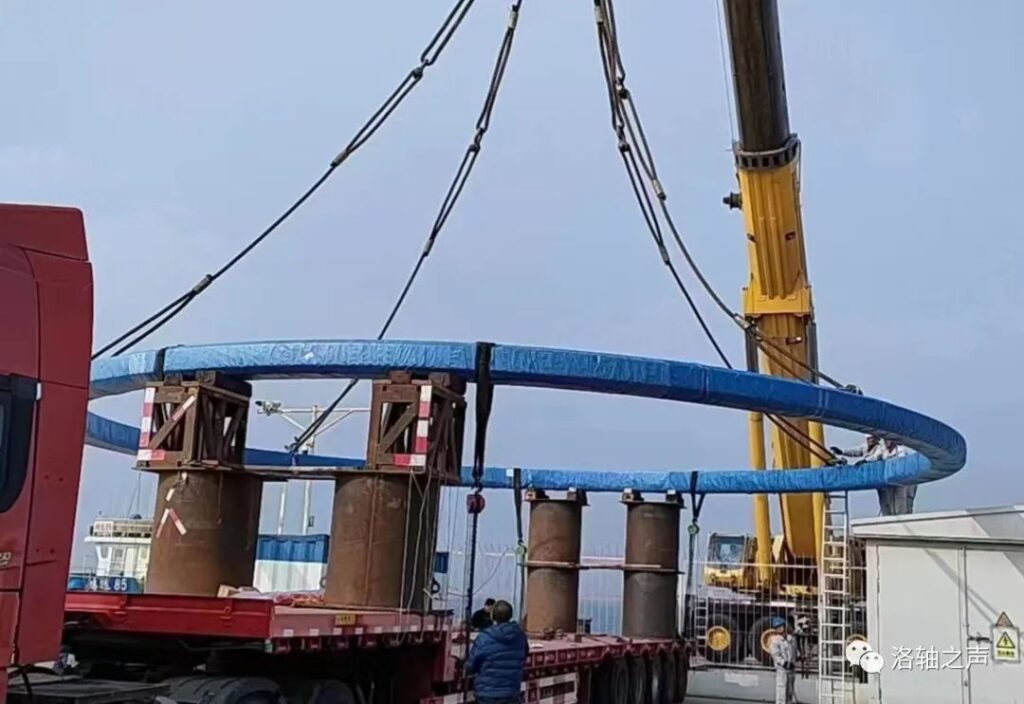
It is understood that the product is matched to a key user of Luo Shaft’s marine engineering for the installation of offshore wind turbine bearings in a 2000 tonne large floating crane vessel.
The product has a large diameter and high precision level, which makes it very difficult to develop and process, especially in the process of heat treatment and quenching stabilisation, which is very demanding in terms of process requirements.
Luoshaft gave full play to its strengths and advantages in technology and research and development, and through a strategic partner in the United Nations, successfully broke through the technical difficulties of heat treatment and other key core process technologies, and finally ensured the successful launch of the product and its successful certification by China Classification Society.
Extended reading:
The “King of Steel”! Breaking import dependence
Domestic bearing steel to help solve
Wind power industry 30 years “neck” problem
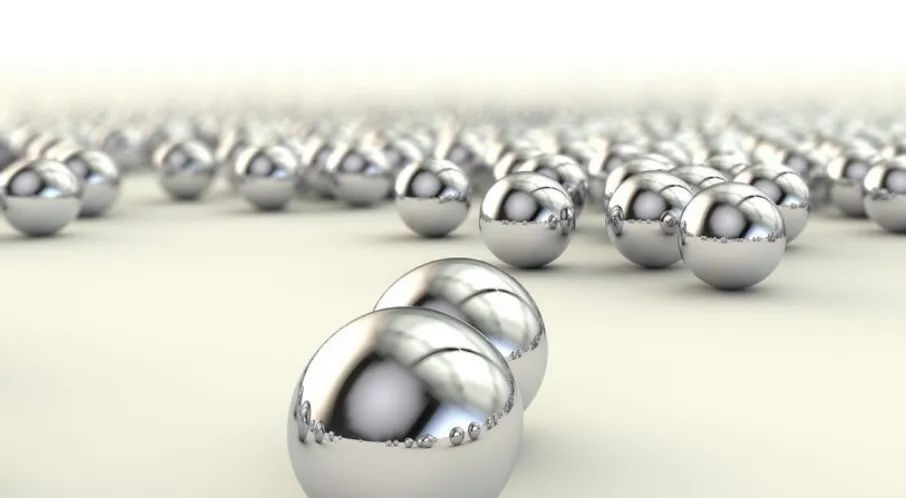
Bearing steel, known as the “king of steel”, is also the steel “joints” of bearings, widely used in wind engines, shield machines, high-speed rail, aircraft, etc., is one of the most difficult to produce, the most stringent product quality requirements, the most inspection items of special steel, once by It has been monopolised by developed countries for a long time.
In the past two years, with the improvement of scientific research capability, the domestic high-end bearing steel has broken the technical barriers and made a number of technical breakthroughs.
\\ Domestic production of 16 MW wind power spindle bearings off the line
Break the monopoly of foreign enterprises as the world’s largest wind power equipment manufacturing base, China’s wind turbine parts and complete machine production has occupied more than 50% of the global market share.
However, an indisputable fact is in front of the Chinese, that is, the key components of wind power has long relied on imports.
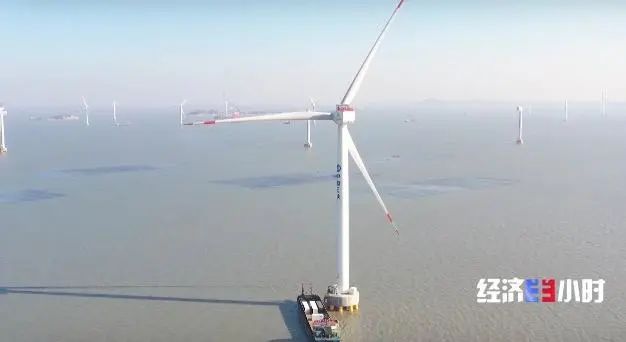
The spindle bearing is the core component of the wind turbine, known as the “heart” of the wind turbine, is the core connection between the generator and the hub transmission parts, due to high technical barriers, the localization rate is low, the domestic market had long been monopolized by foreign enterprises.
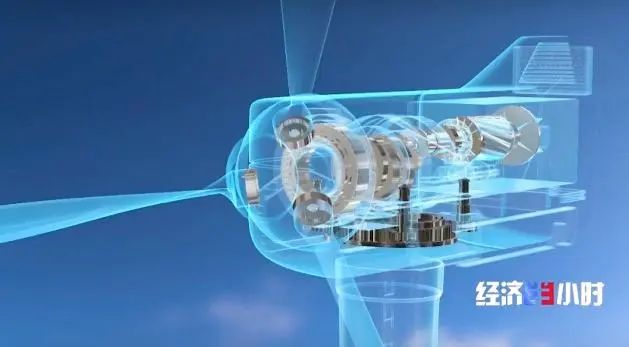
In 2022, a good news from an old bearing enterprise in Luoyang, they manufactured the first set of 16 MW wind power spindle bearings, ending the history of China can not develop and manufacture such high-end products, marking the wind power industry in China for nearly 30 years, the key components “neck” problem solved.
Luoyang LYC bearing Co., Ltd. deputy general manager Zheng Hongwei: this spindle bearing size is also relatively large, the outer diameter reached 3 m 2, this product was previously monopolized by the world’s eight major bearing groups, domestic enterprises research accounted for relatively small, 16 MW bearing development success, so that the domestic wind power spindle bearing from running with the process of running. At the same time, after the successful development of this bearing, the domestic wind turbine to avoid being controlled by others, play a great role in promoting.
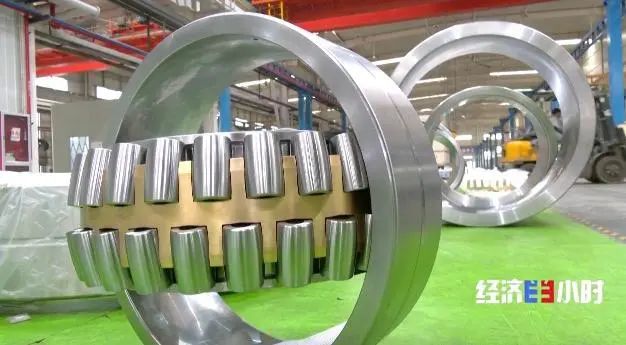
As one of China’s strategic emerging industries, wind power industry plays an important role in the process of achieving the “double carbon” goal, of which the wind turbine supporting bearings as the core key components, its independence, safety, control is related to industrial security, the national economic security of the major events.
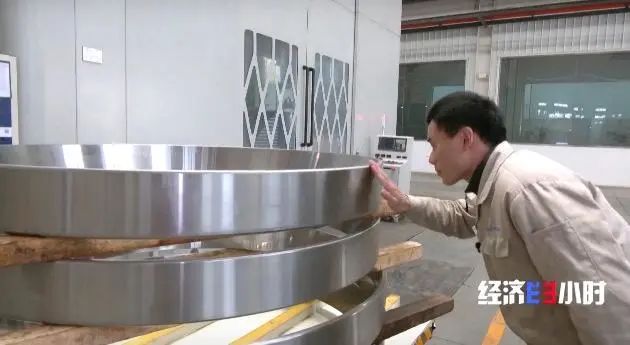
The basic raw material for spindle bearings is bearing steel.
As the most demanding steel in the steel production industry, bearing steel needs “high purity” and “high uniformity” and to control the oxygen content in the steel at a low level, which has been the problem faced by China’s steel enterprises.
Jiangsu Jiangyin an enterprise after years of research and development, the steel inclusions index reached 2.0 below, and ordinary bearing steel, compared with the purity of two to three times higher than ordinary bearing steel, the price is 20% higher than ordinary bearing steel, twice as high as ordinary steel.
At present, their bearing steel has been exported to Germany, France, Japan and other 18 countries and regions.
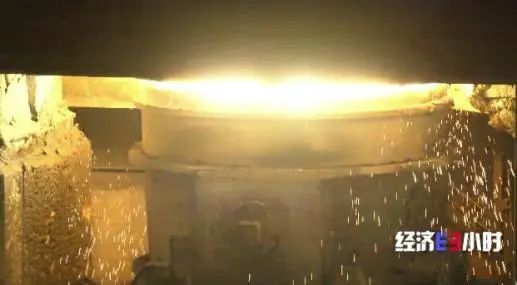
In addition to the steel companies in order to improve the quality of domestic bearing steel and efforts, the General Research Institute of Iron and Steel experts are also in the composition, process innovation to reduce bearing steel inclusions, optimize the composition of steel, and is committed to the industrialization of their research results. China is a large steel country, production is firmly in the first place in the world, but the variety of quality gap can not be ignored. At present, China’s 22 categories of steel products in 17 categories of self-sufficiency rate of more than 100%.
From the point of view of China’s imports of steel, there is still about 20% of the proportion has not yet achieved full independent control. The General Research Institute of Iron and Steel has developed a digital system for this purpose to assist in the development of new materials, which will be open to the public in the future to help iron and steel enterprises and material enterprises to carry out digital and intelligent transformation and achieve the metamorphosis of the iron and steel industry from big to strong.