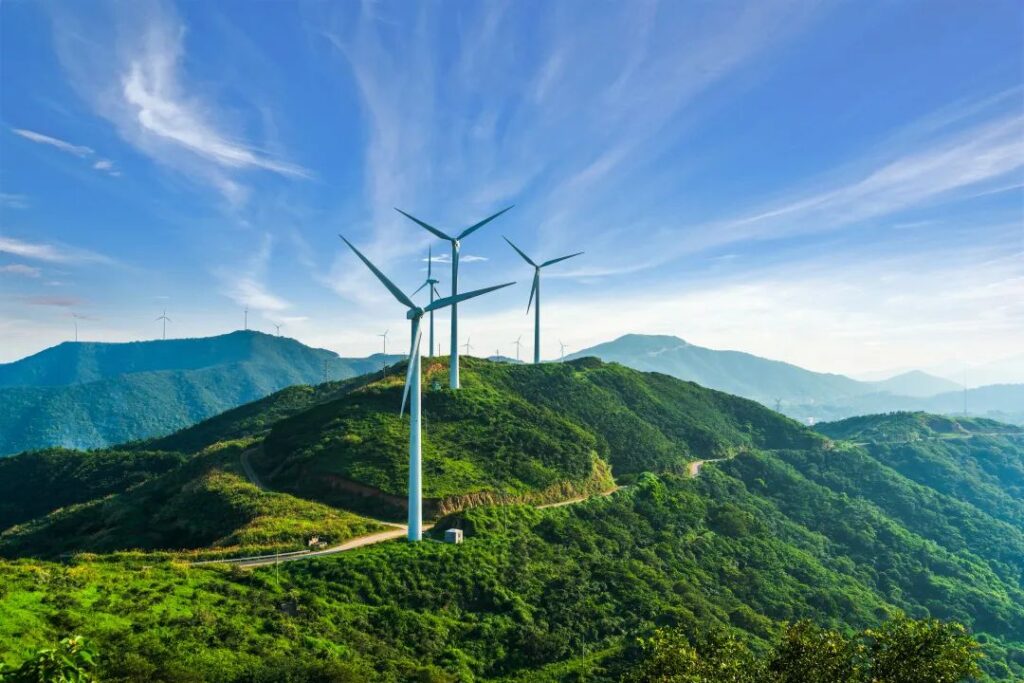
Currently, sustainable development is in full swing, and clean energy sources such as photovoltaic and wind power are gradually becoming the focus of energy transformation and attracting attention – in 2022, China added 49.83 million kilowatts of wind power hoisting capacity, and the cumulative wind power hoisting capacity has reached 396 million kilowatts, maintaining a good development trend.
After the demand has “taken off”, various technologies, products and solution combinations have come together to “hit the ground running”, bringing a “timely rain” for the industry. But is there a guarantee if you encounter problems in the application process? Timken is providing a solid and professional service to protect the efficient and stable operation of the equipment!
A little bit of everyday
Meticulous care
The daily maintenance of wind turbines requires meticulous inspection and observation of internal structures and bearing sounds, but the height of wind turbines, which commonly reach 80 metres, as well as the noise and complex environment faced in wind power operations, make maintenance a difficult task that is too “high”.
However, high standards are not afraid of high challenges, and Timken’s after-sales service is a perfect match for every detail of a wind turbine’s normal operation:
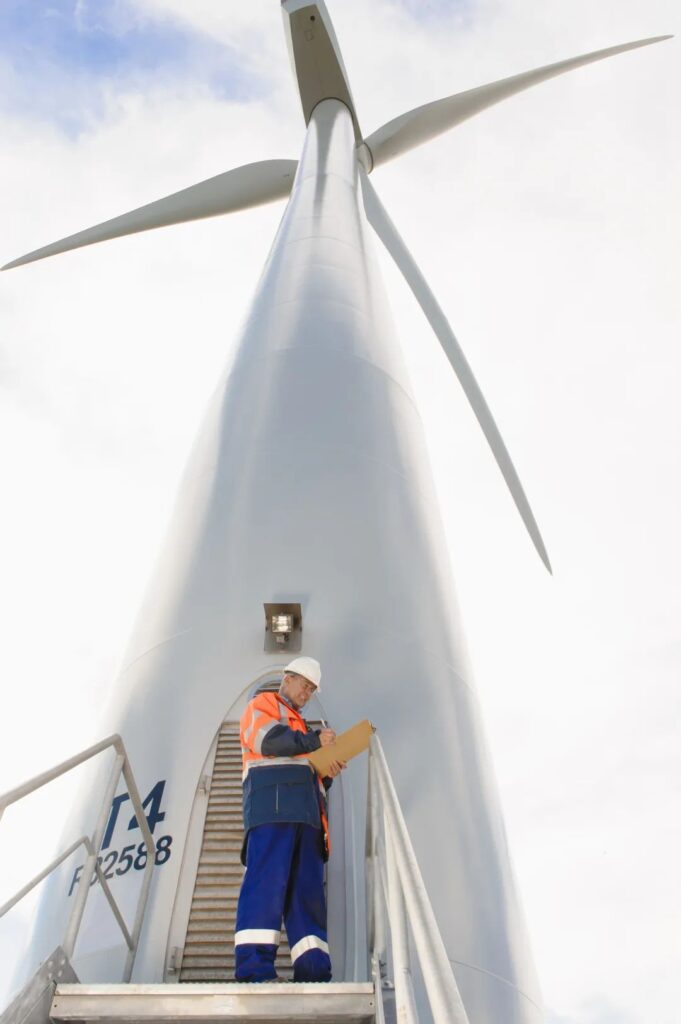
Timken engineers can climb on a turbine in just a few minutes, listen to the bearings and determine the sound to diagnose potential problems; they are experienced in detecting noise anomalies, inspecting bearing vibrations in depth and collecting vibration data for further precise analysis by experts to better solve problems that are not fully visible from the inside; in addition. In addition, Timken also helps customers to check the condition of their bearings during routine maintenance, warning them of risks and recommending the replacement of bearings that have reached the end of their life cycle.
“Iron Tips:
The early wind turbine spindles manufactured before Timken entered the wind power market used mainly spherical roller bearings (SRB), which could be at risk of premature failure before the end of their expected service life. Timken engineers therefore came up with a more reliable, scenario-adapted solution: the use of Timken tapered roller bearings. Tapered roller bearings are designed to extend the service life of spindle bearings and improve fan performance
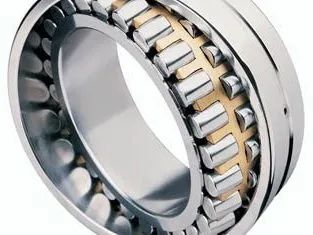
Brass cage spherical roller bearings
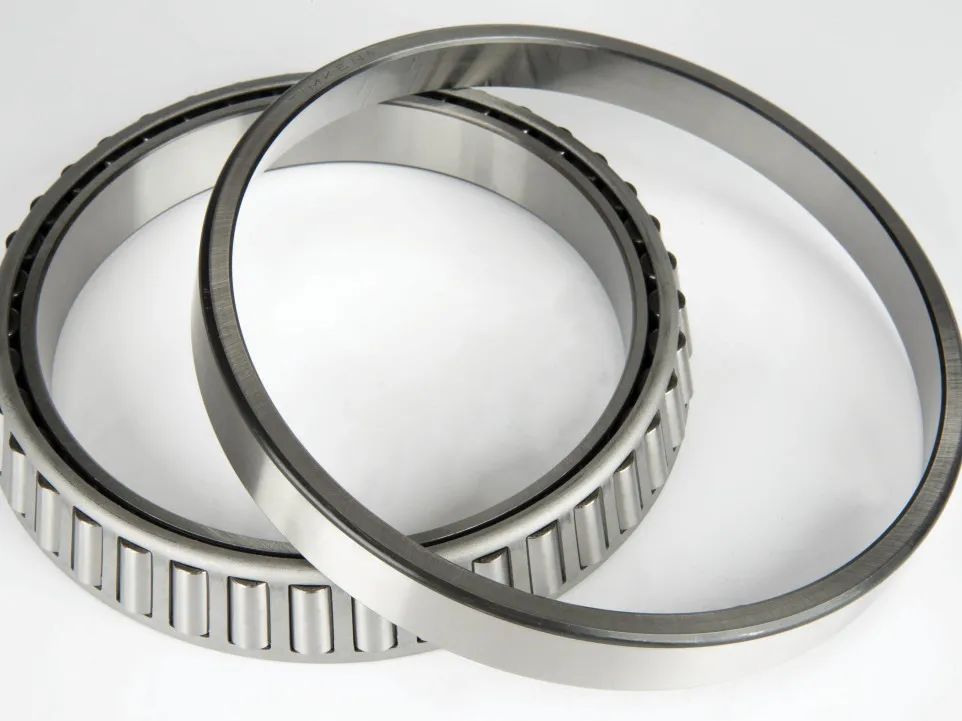
Tapered roller bearings
“Medicine to the disease”
No worries
In addition to routine maintenance, there are many unexpected and unexpected problems that arise when fans are in operation. Some of the problems are in the “head”, but the symptoms are in the “feet”, which makes it difficult to trace the source of maintenance work, difficult to solve, difficult to cure the “difficult problems”.
If you are experienced and professional, you will not be misled by “appearances” and you will be able to investigate the nature of the problem. Timken is an expert in the “nose, nose, nose” approach and is committed to providing professional services to solve the root of the problem and to really get to the bottom of it:
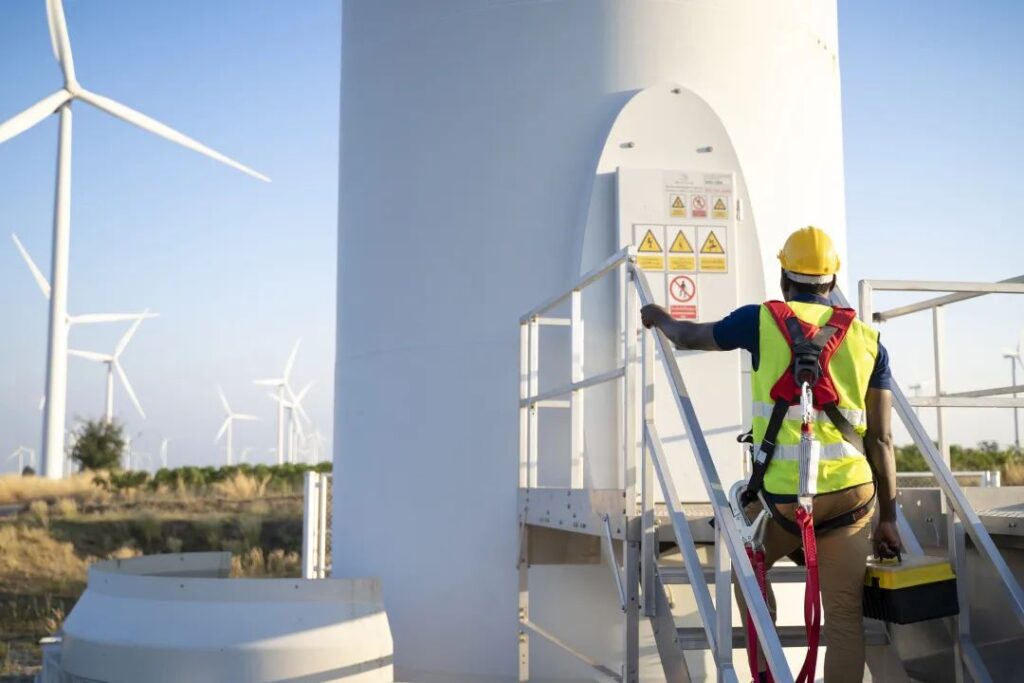
A wind turbine gearbox customer in southwest China had a problem with damage to its high-speed shaft wind turbine gearbox bearings and was desperate for a solution. Timken’s service engineers, with their extensive experience, found that the problem was not in the bearings themselves. After careful analysis of the “cause of the problem” and further understanding of the working conditions, the problem was finally pinpointed to the abnormal operation of the oil pump – not only did this solve the customer’s immediate problem, but also avoided the economic cost of simply replacing the bearing and the possibility of the bearing being damaged again due to a lubrication problem. This not only solved the problem for the customer, but also avoided the financial cost of simply replacing the bearings and the possibility of them being damaged again by lubrication problems.
Tips from the “old iron”:
Some bearing damage will initially point to the performance of the bearing itself, but in such a misguided, often lead to overhaul work “to treat the symptoms but not the root cause”, it is difficult to solve the root of the problem, and can not prevent similar problems from occurring again. Digging deeper into the root cause and reducing customer concerns is a reflection of the value of Timken’s service engineering team and a testament to Timken’s technical strength.
Companionship
Full technical support
As one of the core components of a fan, bearings are closely related to the operating performance of the fan. Often, from the development stage of each new fan model, bearings have become the top priority of the project – design, testing, installation, adjustment ….. Every step of the process is a “technical job” in which a single mistake is made.
At Timken, we believe that careful accompaniment throughout the entire process, from the very beginning, is the only way to create a perfect fit between the model and the bearing. Our quality service goes beyond “fixing” and is a reliable support for our customers with professional level technical support.
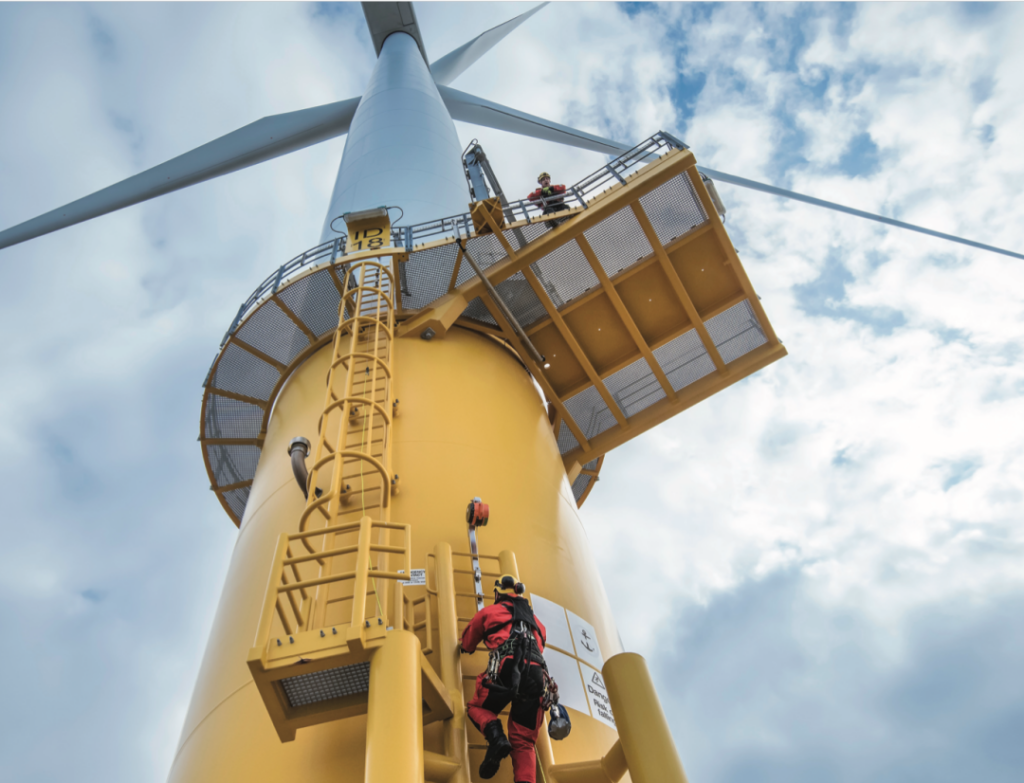
In 021, Timken provided expert technical support to one of China’s first wind turbine manufacturers, a domestic wind power company, in the design of a new model that used tapered roller bearings in the main shaft position for the first time. During the development period, Timken engineers worked with the OEM designers to design, test and install the bearings, providing technical support throughout the process. A manual was also written to detail the proper installation, adjustment and maintenance procedures for the new bearings, better helping the customer reduce economic and time costs in use.
Tips from the “old iron”:
The wind turbine spindle bearings carry blades that are subjected to huge impacts from the wind and therefore need to withstand heavy loads of all kinds. As the size of wind turbines increases, many manufacturers are switching to tapered roller bearings to extend bearing life and cope better with spindle loads.
As a global pioneer in the engineering bearing and industrial drive products industry, Timken understands the importance of innovative product design and scientific installation and maintenance, and is committed to providing our customers with high quality after-sales engineering services to match our high value solutions.
Over the years, our philosophy of “solving complex engineering problems for our customers at all costs” has forged a service engineering capability that is as solid, professional and reliable as our product development and quality production capabilities. We are the “guardian” of our customers in various industries, empowering them in energy, metallurgy, civil aviation, food and beverage and other diverse industries.
In the future, we will continue to uphold our core values of integrity, quality, collaboration and excellence to help our customers in various industries to operate safely and develop efficiently and with high quality!