4 to 20, which is the ratio of the number of manpower distribution in an intelligent workshop to the number of workers operating a traditional production line of the same size;
The daily production capacity of a bearing automated production line is 1400 sets, which is 1.5 times of the manual full-load production ……
The intelligent and digital renewal and transformation of production equipment continues, promoting the gradual improvement of production efficiency, quality and capacity, Harbin Bearing Group Co. is stepping into the fast lane of high-quality development.
In the first two months of 2024, the enterprise signed a new order of more than 700 million yuan, more than the total output value of 2023, which led to a significant rise in corporate benefits.
This year, Harbin Bearing will continue to update and introduce intelligent production equipment and digital systems, accelerating the transformation and upgrading to digital intelligence factory.
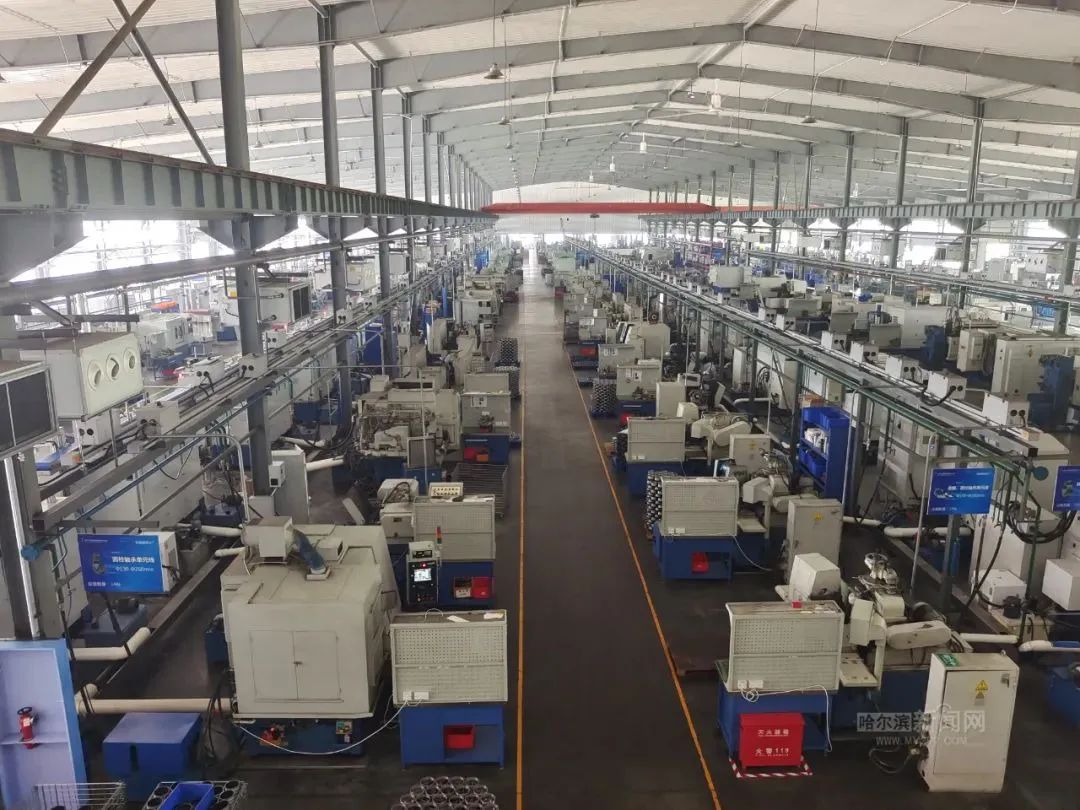
Intelligent arm ‘recognises’ product quality
‘Efficiency’ + ‘quality control’ double enhancement
Harbin Bearing Group Co., Ltd. motor plant, a large workshop bearing processing, assembly production line neatly arranged.
The production line is in operation, only one or two engineers in the control screen monitoring, adjusting data parameters, only metal bearings in the workshop ‘clank’ collision and equipment ‘hum’ running sound … … …This is a far cry from the impression of the traditional factory workshop crowded, workers sweating scene.
‘The manufacture of a bearing, you need to go through the material processing, assembly of the two main links, each link has more than a dozen procedures. Previously, this whole set of manufacturing process requires 20 workers on the production line, but now only one or two people, point and click the screen, you can complete the production.’
Harbin Bearing Group Co., Ltd. engineering equipment division director Nie Xuejia introduced the motor branch introduced an intelligent, automated production line, workers only need to put the original material in the feeding area ….
Intelligent arm on the production line can automatically feed, and thereafter the inner jacket processing, parts cleaning, automatic closing sleeve, loading steel ball, plus cage, finished product cleaning, injection grease, pressure cap, machine light typing and so on more than a dozen processes are all automatically completed by the production line. ‘
After feeding about 40 minutes of production processing time, during which workers will have time to check the equipment operating status, product quality status, to ensure that the normal operation of the equipment, the production of qualified products, and then go to check the other production lines. It can be realised that three or four people manage 12 production lines in the factory.’ Nieologist said.
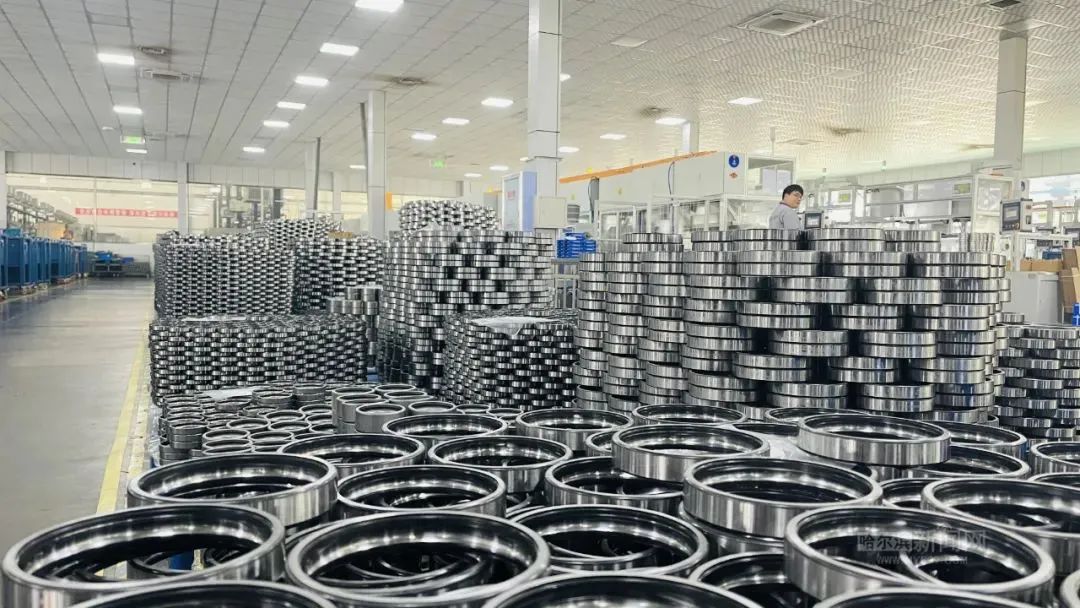
Reporters on the scene found that the most ‘cattle’ motor plant is not automated production, but intelligent feedback.
Usually, the equipment in the process of processing and grinding bearings in the process of the inner diameter, because of the loss of processing tools, will lead to small changes in the parameters of the inner diameter of the bearings, affecting the accuracy of the bearing size of the fitted sleeve.
Just like car brake pads, with the loss of its will be used more and more thin, step on the brake will need to use more power and distance, in order to achieve the same braking distance.
‘Intelligent arm in the grasp of the inner coat for the fit, will automatically identify the inner diameter of the numerical parameters of the change, if more than the standard range, the mechanical arm will be fed back to the front end of the processing end, change the parameters of grinding and processing, to ensure that the rate of the fit.’
Nieologist said, ‘Before you need to manually go to measure and then adjust, now the equipment automatically adjusted, production efficiency increased by 1.5 times, a production line easily 1400 sets of daily output.’
|| The factory is equipped with ‘intelligent brain’.
Remote control of the operation of the situation
At present, Ha axis has completed the investment of 120 million yuan, to achieve the motor plant within the 12 production lines of intelligence, automation updates and upgrades, and for these cold equipment plus the ‘intelligent brain’.
‘The intelligent system is networked with each piece of equipment on the production line, and carries out real-time control of the production beat, task volume, quality process, etc.’ At the factory site, Nieologist said while showing the operation of each production line to the reporter on a large screen.
The system also supports mobile management, Nie can learn through mobile phones to remotely understand the factory’s operating conditions, equipment failure and so on.
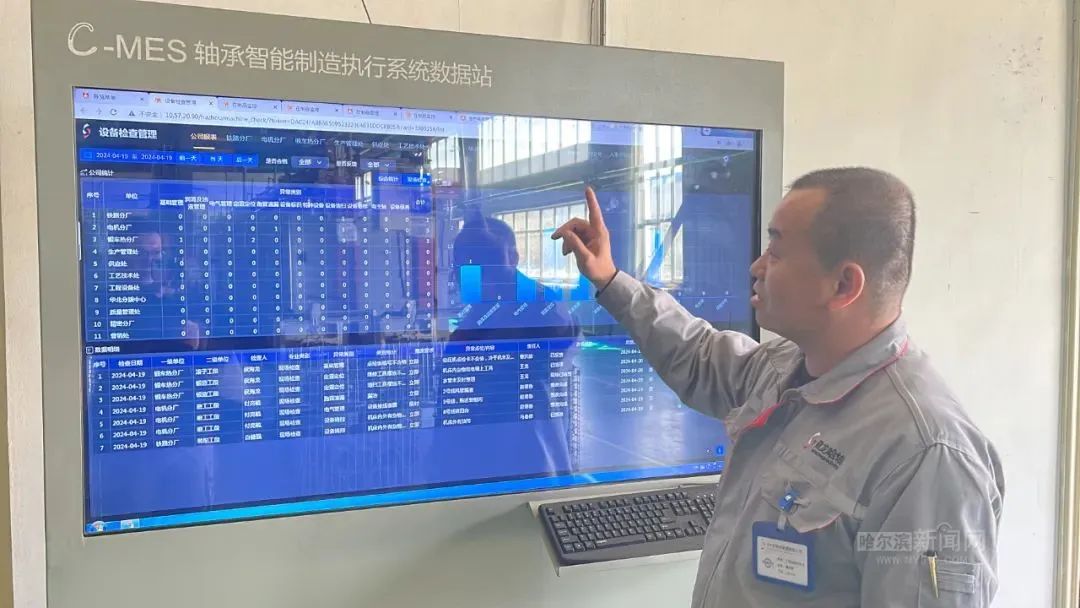
In January this year, Jianlong Group Digital Research Institute built the digital Haaxial production control platform on line, Haaxial all staff on the platform, from planning to implementation to abnormal analysis of data and other production information can be viewed at any time, the realization of the enterprise’s digital management, greatly improving the production efficiency.
At the same time, the digital Ha axis production control platform also built on the improvement of the improvement platform, each employee found any problem, can be submitted to declare the relevant recommendations.
‘’Intelligent‘ manufacturing liberates employees from simple physical labour and puts more energy into production management, innovation and market development.’ Nieologist introduced, this year, Ha axis from the production, technology and other multi-dimensional and customer depth binding, increase the viscosity of customer demand.
As parts supporting enterprises, ha shaft to maintain order delivery and host enterprise production rhythm consistent; in technology closely follow the host enterprise demand, rapid technical improvement and innovation, the first time to meet customer demand, to do with the host enterprise common development, to achieve the maximisation of the interests of both sides.
‘The changes in the enterprise in these years are visible to the naked eye, and it is transforming into an innovative enterprise, an operational enterprise, a digital enterprise and a beautiful enterprise, and the production situation is getting better year by year.’ Nieologist said.
Ha axis this year plans to complete the total output value of 1 billion yuan, an increase of nearly 50%. In the first quarter of this year, Ha axis has achieved output value of 175 million yuan, while the first two months signed a new contract amounted to more than 700 million yuan, to achieve the opening of the door.
| The old factory ‘digital intelligence’ for the new
Towards high-quality sustainable development
Enterprise digital, intelligent transformation and upgrading, help the production and market development of Ha axis steadily forward. This year, the shaft will continue to press the ‘fast-forward button’ for the intelligent upgrading of enterprises.
‘We will also invest 10 million yuan, the purchase of more than 30 robotic arms and two AGV unmanned carriers, to achieve transport, loading, feeding all intelligent, greatly improving production capacity.’
Nieologist told reporters that 70% of the labour force in traditional factories are used for ineffective handling, each person daily handling volume of 1.5 to 2 tons, and intelligent, automated equipment updates, the labour force is freed to improve efficiency and production capacity, but also reduces the labour force and operating costs.
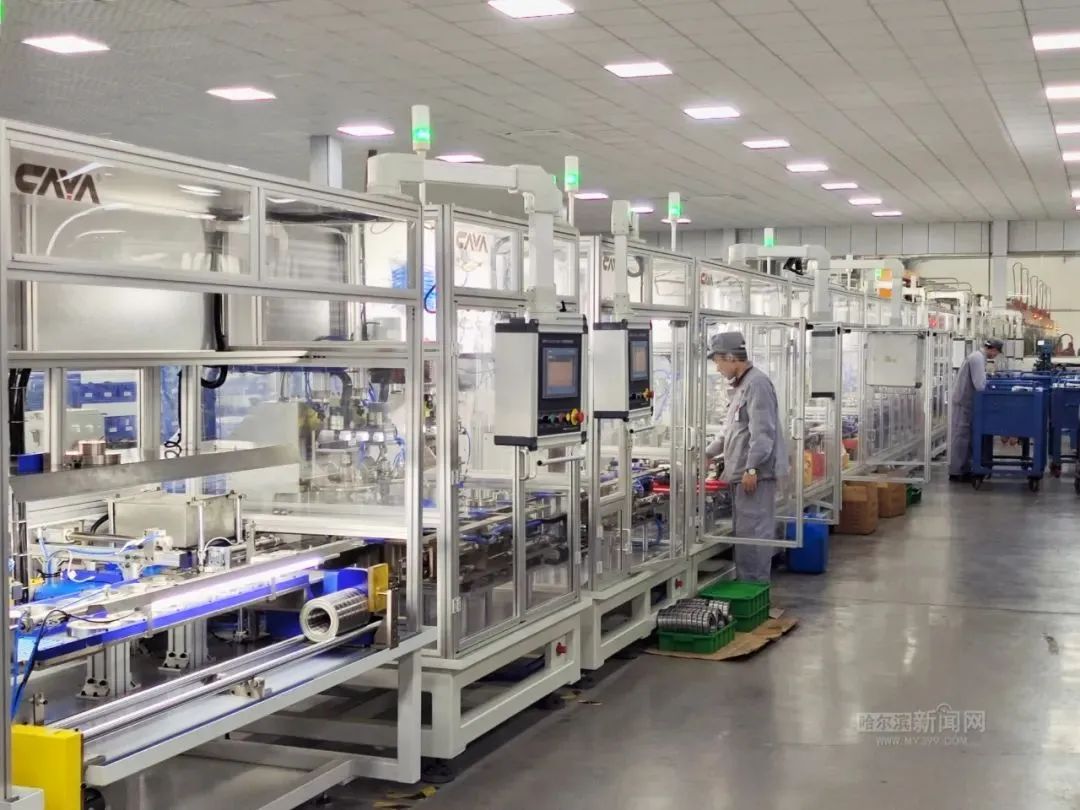
Taking AGV unmanned vehicle as an example, a single vehicle can carry 1 tonne of heavy materials at a speed of up to 2 m/sec. Through efficient task scheduling, scheduling algorithm optimisation, high-precision two-dimensional positioning technology, you can schedule multiple AGVs to work at the same time, compared with manual, AGV unmanned vehicle transport efficiency increased by 50%, to achieve the maximum handling efficiency and quality.
Reporters in the Ha axis motor plant to see, at present the enterprise has introduced an AGV unmanned truck trial, workers only need to put the bearing inner jacket in the car, it can automatically travel to the feeding area, by the mechanical arm for feeding.
Today, Ha axis group is accelerating to digital intelligence, unmanned plant transformation and upgrading, some products by software optimisation analysis design, loaded test, the indicators have reached the level of imported high-end products, and actively build innovation leading enterprises.
Up to now, Ha axis has a national enterprise technology centre, three provincial enterprise technology centre, a provincial engineering research centre, and so on, and through the digital (intelligent) demonstration workshop in Heilongjiang Province, Heilongjiang Province, the manufacturing industry, such as a single champion identified.
Recently, the Heilongjiang Provincial Department of Industry and Information Technology also issued an honorary certificate of Heilongjiang Provincial Manufacturing Innovation Centre Enterprise for Haaxial, marking that the company has been highly recognised by the society in terms of industrial science and technology innovation.