Every day, Timken service engineers may receive requests for help with breakdowns in a variety of industries. Faced with a variety of problems, they must quickly and accurately determine and troubleshoot the problem to get the equipment back up and running.
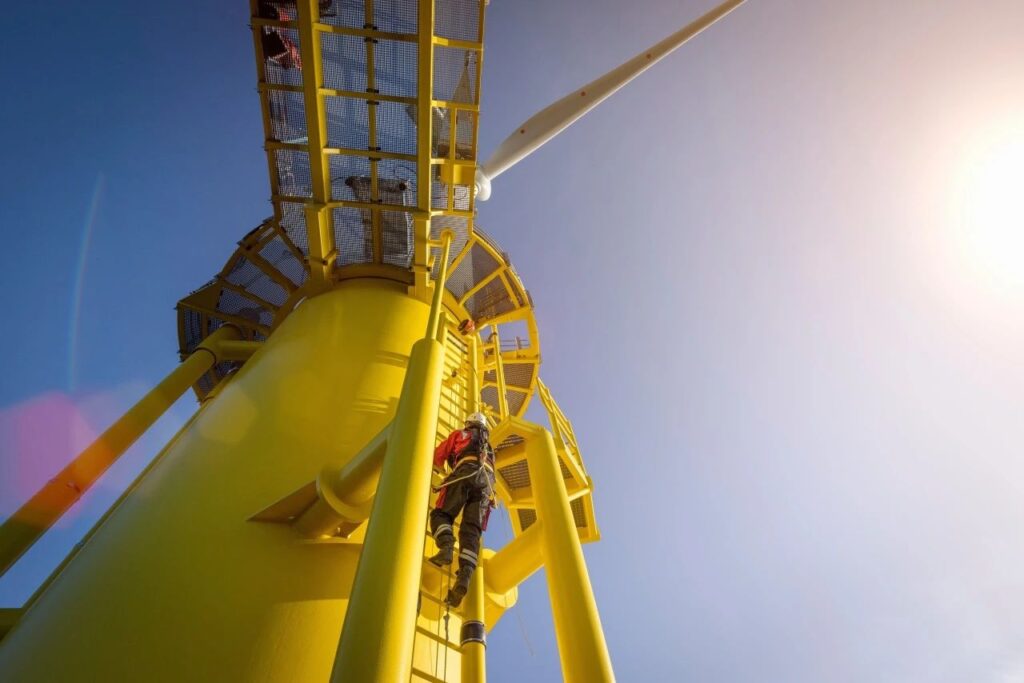
- The Best Engineering Services – Avoiding Problems
In a fast-moving industrial system, equipment downtime can mean higher costs, business disruption and even damage to customer reputation. For more than 125 years, Timken’s bearings and drives have been on a mission to ‘keep things running’. Service engineers around the world know that preventing risk is better than fixing it.
They are committed to early intervention and risk management. For example, they helped a metallurgical customer solve a problem of excessive bearing clearance caused by improper mounting. Just by correcting the operation process, the service life of the bearings was doubled, and the customer was helped to reduce the replacement of about 200 sets of bearings in five years, saving costs of 4 million yuan. Even the slightest deviation in bearing mounting can have a huge impact on bearing life, so the process requires a high degree of knowledge and operational precision.
Another Chinese heavy-duty truck customer is using Timken wheel bearings for the first time. Heavy-duty trucks carry extremely heavy loads and operate in an extremely complex environment. The cost of a wheel strike is unimaginable.
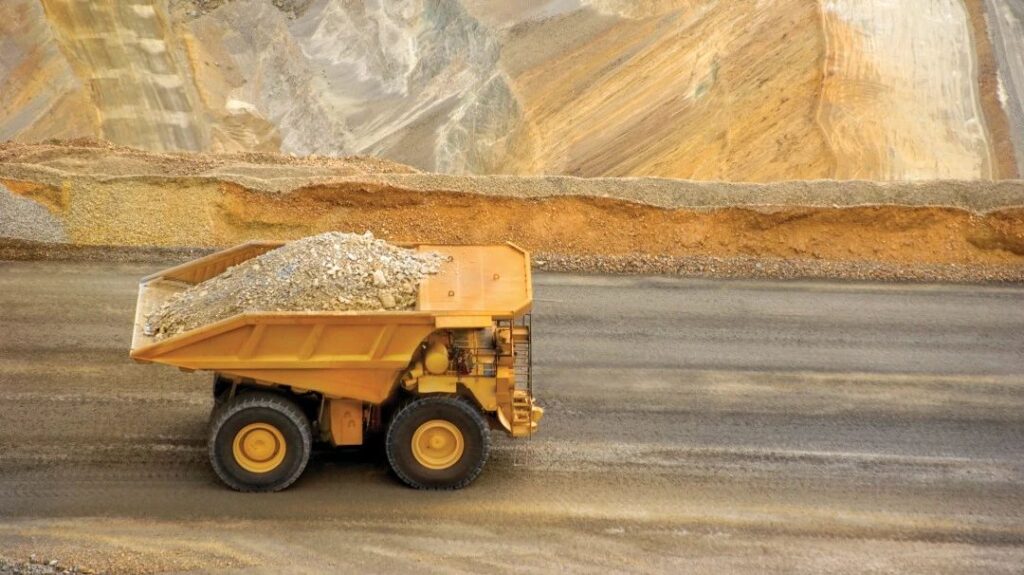
Timken’s service engineers went to the site at the first time to provide comprehensive training for the customer’s staff, guiding the use of Acro-set to adjust the front wheel, the push-pull method of adjusting the motorised wheel, and installing the bearings in strict accordance with Timken’s recommended operations. The on-site technical support ensured the smooth installation of the bearings and avoided the later damage caused by improper clearance setting. After the installation was completed, Timken service engineers also provided operation manuals to help customers cope with unexpected situations.
In the field of wind power, in order to assist a customer in completing the installation of planetary wheel and planetary carrier bearings in a wind turbine, service engineers were stationed for three consecutive weeks, participating in and accompanying the whole process from lifting to debugging, and assisting the customer in improving operational safety and efficiency.
This type of service may seem unusual, but it avoids major losses that could occur in the future. Timken always insists on the simplest and most reliable way to reduce risks.
- When failure occurs – 7 * 24 hours attentive guarding
When the equipment is put into operation, the bearings start to face the real working conditions, and all kinds of damages are unavoidable. Determining the cause of failure is often the most challenging and critical step in the service.
A heavy industry customer has been suffering from unstable equipment performance for a long time, and frequent replacement of bearings has not helped. Timken engineers found that the problem was with a bearing of another brand. The design was flawed – the outer ring had an interference fit with the housing, creating additional radial loads. The engineers recommended a change to a looser fit, which solved the longstanding problem.
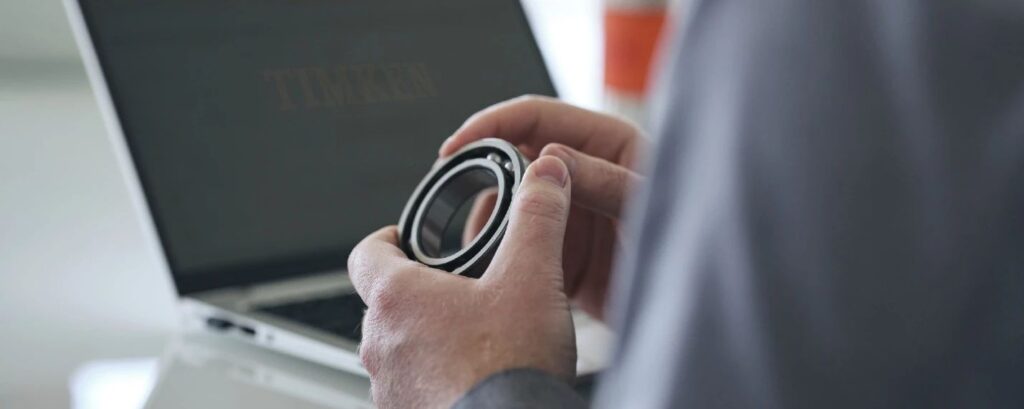
Statistics show that most bearing damage is not caused by defects in the product itself, but by improper installation, lubrication, environment or maintenance. Accurately assessing the condition of bearings and inspecting them regularly can significantly improve the stability of equipment operation.
In the oil and gas industry, a customer asked Timken service engineers to check whether two sets of bearings that had been in operation for five and six years were still serviceable. After an on-site evaluation, the service engineer found that both had suffered severe abrasive wear due to mud intrusion and recommended that the customer scrap them immediately. Continued use would have resulted in higher repair costs.
Timken has also developed a variety of engineering tools to make service more efficient. For example, Syber™ analysis software evaluates the impact of the environment on bearing life and performance, optimises preload and lubrication options, and provides a scientific basis for customers.
- Enabling Engineering Services with Intelligence and Digitalisation
With the popularity of intelligent and automated equipment, Timken’s engineering services are also keeping pace with the times and continuously promoting the digital transformation of the engineering services industry. Through training professionals and organising industry training, we enhance our customers’ ability to manage new equipment.
Timken also enriches and improves online engineering service tools, realises cross-region rapid response, combines on-site service with remote monitoring, and provides customers with smarter operation and maintenance support. With the global service network and experience database, engineers are able to quickly diagnose difficult problems and make things easier.
In addition, Timken has launched the Engineer for a Day programme globally to develop the next generation of problem solvers and promote sustainable talent development.
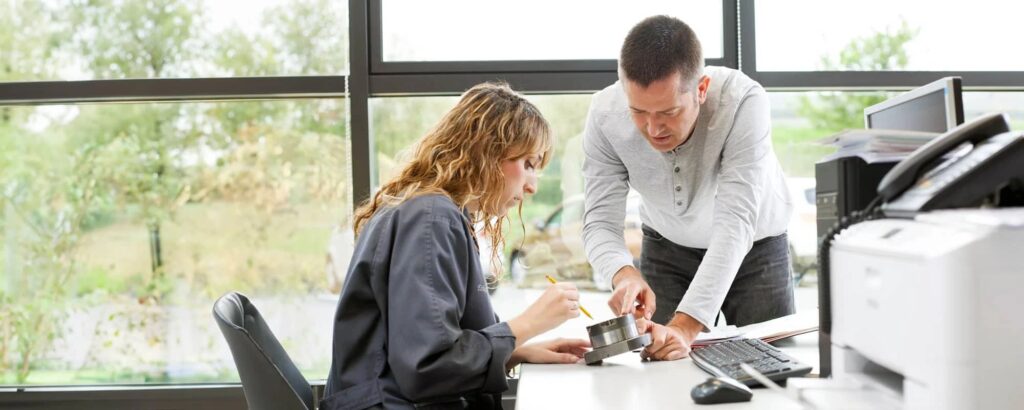
Timken’s global service engineers are trained under a uniform system of excellence, which ensures that customers receive a consistent, high-level service experience no matter where they are. A century of engineering experience is an asset to our customers.
From the shop floor to extreme environments, from current failures to future challenges, Timken’s engineering services team relies on leading-edge engineering support and a global service network to provide customers with accurate, efficient and sustainable support that makes every operation more reliable.